Best Practices for Retaining Aircraft Mechanics
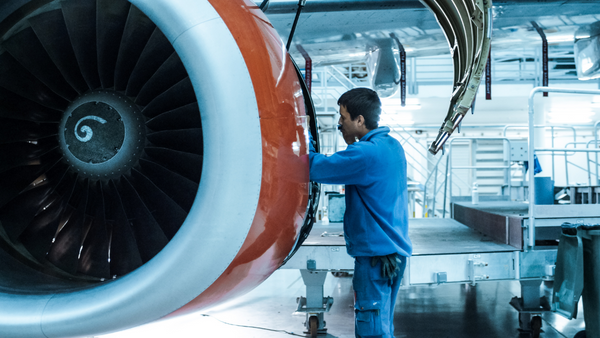
As part of our series on attracting and retaining aviation maintenance technician (AMT) talent, we’re looking at how to retain our already-established workforce.
The industry has taken a lot of hits over the past 30 months. But there isn’t any way you can’t get beat up when the worldwide fleet is grounded. However, this industry's problems were well established before 2020; the global pandemic only served to exaggerate a problem already there.
Now that we’re in this mess, we must focus on what we can do to keep our existing workforce together. What are their pain points? What do they need to stay in this career instead of retiring or leaving to do something else?
Roadblocks to Technician Retention
Let’s address the elephant in the room first.
COVID-19 is still fresh on everyone’s mind; it will be long before we forget about the rows of airliners parked while the runways were abandoned and the terminals empty.
We also haven’t forgotten about the furloughs that struck workers as the bailouts expired. As soon as those financial life rafts deflated, thousands of workers were sent packing. Frankly, we have little right to act surprised that a bad situation ended up becoming a whole lot worse.
The airlines, aircraft manufacturing, and the industry have long wrestled with furloughs. When traffic wanes, you have to do something with excess employees. After a while, people have enough and would rather stake out doing something else.
Leaving Options On the Table
Also, let’s look at the largest talent pool of potential mechanics: the military. Every year there are about 200,000 members leaving the ranks. Mind you, these come from all types of backgrounds, but odds are that a few thousand of them are aircraft maintainers. Not aggressively tapping this talent pool is as important as retaining talent.
Why?
Allow us to explain. A civilian attending an Aircraft Maintenance Technician School has only the theoretical experience to pull from and the labs performed on example aircraft.
A separating military technician has at least four years of experience in the field. He or she likely worked 50-60 hour weeks routinely, with many weeks cracking 70-plus hours. He or she has worked in the worst conditions and extremely technically demanding aircraft, far more so than a standard B737 or A320. Also, depending on his years of service, the military technician may have already worked on four or five different airframes. They know how to learn about new airframes and new systems in a short amount of time.
Aircraft maintenance operators have got to aggressively go after these folks. They have no false allusions about the job, and doing it as a civilian is much more pleasant and low-key than in uniform. These folks have changed engines while taking enemy mortar fire. Surely we can lure them into working on Boeings in an air-conditioned hangar.
The Great Resignation
The aviation industry could not expect that it wouldn’t be affected by the Great Resignation.
The Great Resignation is a wild phenomenon. It is the highest overall resignation rate by a wide margin in the last two decades. The part that makes it even wilder is that it was predicted, and it continues to persist.
Employees are leaving in droves, and why not? There are practically permanent positions to fill because so many have been vacated. It is the perfect opportunity for someone to leave a job they are tired of or a vocation they don’t like and try something new. They see it as low risk because their odds of being picked up are so good.
When you consider a career like AMTs, where they have invested so much time, energy, and capital just to get into the job (earning their A&P), only to watch it vanish in a furlough, you can understand why they would like to try something else.
Unfortunately, the flip side of this is that aircraft maintenance operations cannot simply hire in people off the street to fill holes since there is such a high threshold of entry.
Work/Life Balance
Airlines fly constantly, and their ground crews work the same hours. If you work line maintenance, you will eventually end up on a shift outside normal working hours.
The best pay and incentives are in the major air carriers, which attract talent, but the converse is that workers may have to sacrifice work-life balance for it.
.png)
What Are We Going to Do About it?
As stated earlier, we must attract the right candidates to fill the ranks. Frankly, military members are used to working terrible hours, having no say in their shift schedule, deploying for months on end, etc. A lot of them love the work but hate what comes with it.
When recruiting this demographic, we need to promise something that resembles normalcy but lets them do cool stuff they love (running engines, working on huge jets, etc.). The threshold of entry is quite a bit lower for veterans, and sponsoring them to go through an A&P prep course or conducting one in-house as part of an apprenticeship would go a long way towards securing techs with proven and verified backgrounds in heavy jet maintenance.
For the current AMTs already in the ranks, we have to keep them there, especially those too young to retire. The mid-career tier that could be lured into the Great Resignation is a prime demographic to keep on board. They have the experience and knowledge to be autonomous but are young enough to start over.
- First, pay them more if we can, or reward loyalty in some tangible way.
- Second, give them the tools to work autonomously.
- Third, work on recruiting talent (see above) to lighten the load on these AMTs.
The ops tempo is back to pre-pandemic levels, but the workforce isn’t. They need manpower, and there is no metric that matters besides more AMTs, but preferably AMTs who already know the score and don’t have to be walked through every task.
Wrapping Up
The future looks a little bleak for AMTs, but it doesn’t have to. We have tools that provide value beyond anything this workforce has ever seen. Hours spent in zero-sum work in the past (trying to get a signature or tracking down parts in the supply chain) can now be put back into productive work. We have the solution to most effectively employ your current talent pool. As your workforce grows, we’ll grow with you to accommodate your demands.
AireXperts is committed to helping your operation get back on track, retaining the talent you already have, and onboarding new talent.
Give us a call to set up a demo to see what we can do for you!
Subscribe for updates
Every fact, every interaction, every choice and every voice. In one place.
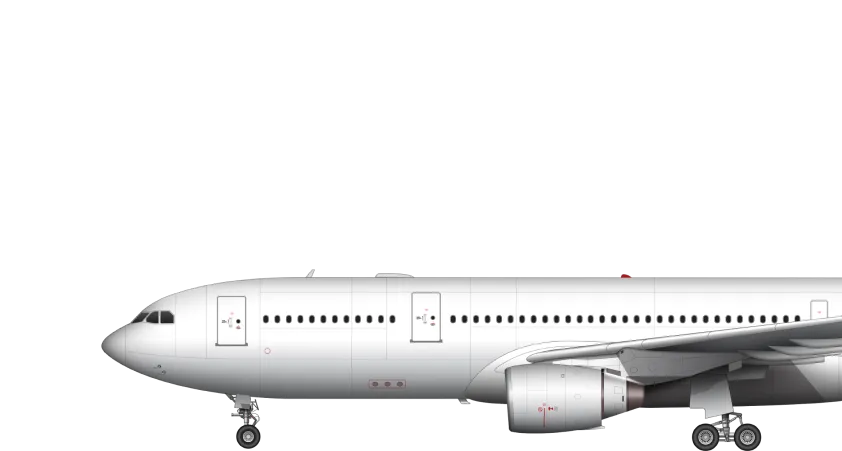