Uniting Aircraft Maintenance Teams Through Structure, Organization and Communication
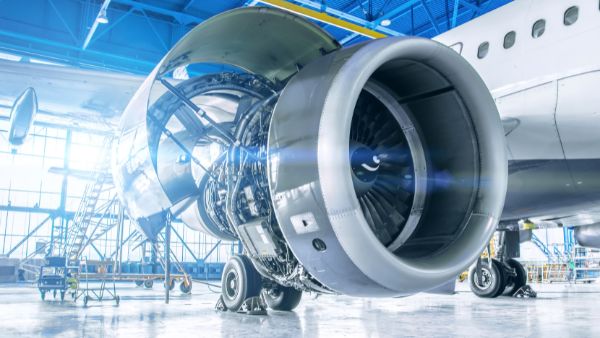
It has become clear that there are serious problems facing the aviation industry, namely the airline industry. Over seven thousand flights were canceled over Memorial Day Weekend. Fuel prices are hitting all-time highs, with nearly a dozen price hikes this year alone.
And these are just the problems that we are witnessing in plain view; it doesn’t take into consideration what has been going on behind the scenes for years leading up to this. Major technician and pilot shortages are no longer looming, they are here.
Understanding that manpower shortages are not fixable in the short term, MRO and airlines need to focus on streamlining work processes with their existing workforce, and retaining the staff they have. Uniting maintenance teams through structure, organization, and workfloor communication are practices that promote higher efficiency and workforce cohesion, practices that we specialize in.
The Problems Facing the Aviation Industry
Sugarcoating the problems in the industry isn’t cutting it anymore. If there is anything we have collectively learned over the past two years, it is that the world moves through the air, and is only growing more reliant on air travel.
Boeing anticipates an overall global freighter fleet in 2040 will be seventy percent larger that the freight fleet in pre-pandemic times. The global demand for new technicians over the next two decades will be 626,000, and the demand for pilots will be just shy of that. That will require some 31,000 new technicians annually to be sustainable.
Unfortunately, the news in the industry is not altogether good news. The Aviation Technician Advisory Council (ATEC) anticipates that the number in the U.S. over the next two decades will fall short of its goals by roughly twelve thousand technicians. But the problem has been broadly ignored; many outlets were warning of the impending technician collapse as long as four years ago. In 2018, over a quarter of the mechanic workforce was over 64.
The problems are being illustrated in real-time. We can see them manifesting. The question now is what to do about it? Truthfully, everything in aviation revolves around the technical side of flight. Obviously, pilots are critical, but they are pedestrians without operational aircraft.
The Problems Facing Maintenance Teams
Half of aircraft maintenance is documentation. That is just a wag; it really might be more like ninety percent. All of us who cut out teeth (and knuckles) on jets know that you can and will spend hours on a repair only to spend more hours on supply requests and proper documentation. It is a never-ending cycle.
One of the most frustrating parts of being an aircraft mechanic is seeing technology advance all around you (iPhones, Android, IoT, etc.) and being helpless to employ these technologies in your work. You can easily envision how much it would help and could streamline the process.
Think about the possibilities:
- You have a secure app that allows you to sign off maintenance tasks as you do them. You can use biometrics to certify the work done, on the spot, with your smartphone.
- The ability to scan a QR code tagged on individual parts (actuators, engines and engine accessories, APUs, and especially tires and wheels) and immediately take you to all of the pertinent data for that part. Illustrated parts breakdown, specifications, and supply request. You can place a supply request by pressing a button and order the new part against the defective part, which would be loaded on the QR.
- Using your camera on your phone to record visual damage and upload those images along with the discrepancy to ensure the problem is easily identified by specialists.
Instead, technicians are still predominantly recording maintenance via paper-based systems. We can do better.
AireXpert is committed to creating solutions that streamline processes so we can get the most efficient use of time out of our technician workforce. We can’t make the workforce bigger and more proficient, but we can give them the tools they need to optimize their work.
Streamlined Flight and Ground Ops Communications
The goal of our software is to streamline the flow of communications between the flight deck and maintenance control. It’s a stressful environment. Passengers get irate at the drop of a hat. It gets hot sitting on the ramp on only air from the APU.
If the flight crew isn’t able to accurately articulate the problem at hand into an actionable discrepancy, it adds time to the troubleshooting process. This can be the difference between still making an on-time takeoff and a lengthy disruption.
Our system allows flight crews to upload photos and videos to our platform, providing the added dimension to troubleshooting that has been lacking since the first A&P picked up a wrench.
Imagine how useful it is to attach a 30-second video of the gauges when trying to start an engine instead of just stating “hung start.” This is game-changing technology that AireXpert is at the forefront of.
Also, the information is loaded against specific aircraft registration (‘N-numbers’) numbers, assuring technicians and maintenance control that the information they are receiving is assigned to the correct aircraft.
How to Structure a Maintenance Organization for Better Communications
Every technician learns to use the right tool for the job. The use of communications and maintenance documentation tools is no different. It is time to trade in the “No. 2 wrench” for a digital solution that streamlines the flow of information and provides evidence of accountability.
Documentation is a time-consuming but necessary part of the maintenance process. We can’t do anything about the necessity of proper documentation, but we can address efficiency.
We know that a byproduct of a dwindling workforce is a larger share of the workload for the remaining techs. Unfair, yes, but it is where we stand.
By nature, this job entails a lot of independence. You are moving from jet to jet, addressing discrepancies for long hours. A lot can change from the shift briefing to the end of the day.
A mobile application is just the ticket to keep all of your technicians on the same page. It allows you to push mechanical issues as they develop and to rack and stack them based on priorities. It allows all of the technicians to see the status of the jets, and identifies which issues are in work and which are awaiting action. Armed with this information, supervision and maintenance control are better able to assign technicians to open tasks based on priority.
Conclusion
There are no easy solutions to the technician and pilot shortage crisis. And yes, let’s call it what it is: a crisis. AireXpert is here to allow your existing workforce to work better and smarter by equipping them with the tools they need to focus on diagnosis and repair, rather than administrative issues. Any time that it keeps techs on the aircraft rather than the computer room is a decisive victory for your organization, and it will surely keep your technicians happier, too.
To get a better idea of what AireXpert can do for your organization, give us a call and we can set up a demo for you and your organization!
Subscribe for updates
Every fact, every interaction, every choice and every voice. In one place.
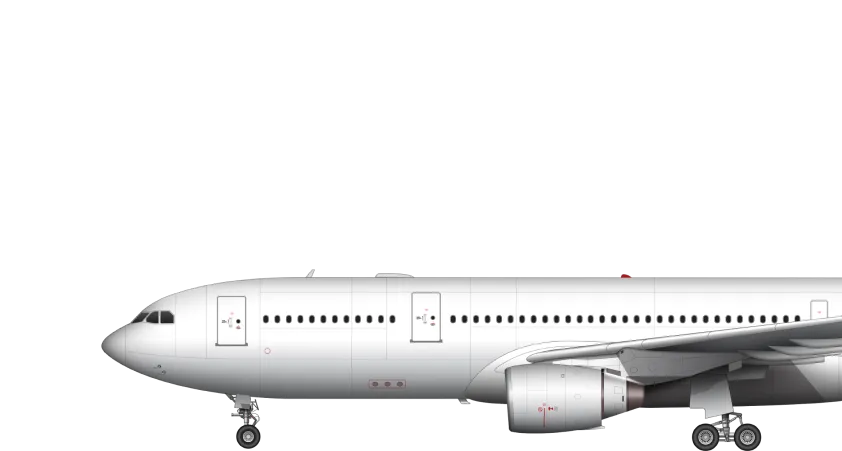